Using Structural Analysis Software from Ansys to Overcome Random Vibration
“Utilizing Ansys Mechanical and Sherlock analysis has been instrumental for us in aligning environmental test outcomes with analysis data. This correlation has proven essential in pinpointing potential failure modes throughout our product development phase. It’s become indispensable in our design cycle, ensuring our product aligns with the rigorous demands of the space environment. Qfinsoft has also played a crucial role, not just in providing the necessary tools but also in offering valuable support and guidance to our engineers.”
—Shane Martin, Mechanical Design Lead, NewSpace Systems
When designing components for the space environment, significant attention must be put into designing for intense vibration, shock, and thermal environments. During the development of a new reaction wheel, NewSpace Systems (NSS) conducted extensive environmental testing to examine the performance and predict the lifetime of the wheel. Special attention was to be given to the electronics and bearings, as these components had the most significant impact on the lifetime of the wheel.
Challenges
During the development phase of a new reaction wheel, an electronic device failure was identified during vibration testing. Ansys Sherlock reliability analysis software was used to simulate the vibration environment on the printed circuit board (PCB), which identified the root cause of the failure to be due to a specific resonant mode on the PCB, which coupled with that of the chassis.
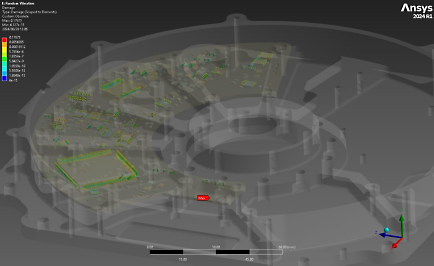
Figure 1. Fatigue damage assessment on PCB
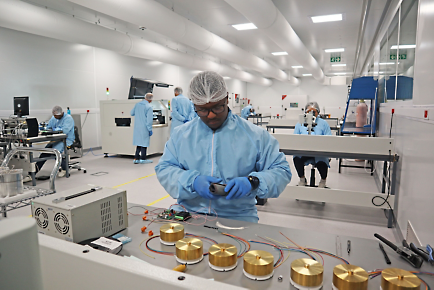
Figure 2. Reaction wheel production in cleanroom
Engineering Solutions
To address the failure mode of the component, NSS followed a combination of two solutions. The first was to add additional mounting points to the components’ PCB to increase the frequency of its resonant mode so that it fell outside of the damaging vibration spectrum. Secondly, the chassis the PCB was secured to was stiffened to increase its resonant mode and reduce the deflection of the chassis under vibration. NSS assessed and optimized the combination of these solutions with Ansys Mechanical structural simulation software’s random vibration analysis on the chassis and PCB. They then assessed both the total deflection of the chassis and fatigue lifetime of the leads of the electronic components.
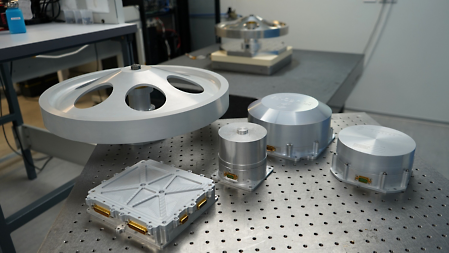
Figure 3. NSS reaction wheel family
Benefits
By being able to simulate both the original design and the new, optimized design, NSS implemented engineering improvements that reduced the chassis deflection by 24% and increased the fatigue lifetime of the electronics by 686%. The new solution was then manufactured and tested successfully.
Technology Used
- Ansys Mechanical™ software
- Ansys Sherlock™ software
Company Description
NewSpace Systems (NSS) is a trusted multinational manufacturer of spacecraft components and subsystems. Headquartered in South Africa, it operates branches in North America, Europe, and Oceania. As leaders in guidance, navigation, and control (GNC) products, NSS supports the majority of commercial spacecraft manufacturers, including several blue-chip companies and constellations of more than 500 satellites. To date, NSS products have been utilized on more than 2,000 spacecraft.
NSS is focused on delivering high-quality solutions and services. Whether offering clients access to flight-proven, off-the-shelf GNC products or working closely with clients to develop custom solutions, the NSS team understands that each mission is unique and strives to ensure the success of their partners through close collaboration.
Related Posts