VIBRATION AND SHOCK ANALYSIS OF A PCB WITH ANSYS SHERLOCK: “Predicting FPGA reliability and robustness”
Utilizing Ansys Mechanical and Sherlock analysis has been instrumental for us in aligning environmental test outcomes with analysis data. This correlation has proven essential in pinpointing potential failure modes throughout our product development phase. It’s become indispensable in our design cycle, ensuring our product aligns with the rigorous demands of the space environment. Qfinsoft has played a crucial role, not just in providing the necessary tools but also in offering valuable support and guidance to our engineers.
Senior Mechanical Design Engineer, Shane Martin
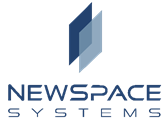
NewSpace is a trusted multinational spacecraft components and sub-systems manufacturer headquartered in South Africa, with branches in North America, Europe, and Oceania. Leaders in the area of Guidance, Navigation and Control (GNC) products.
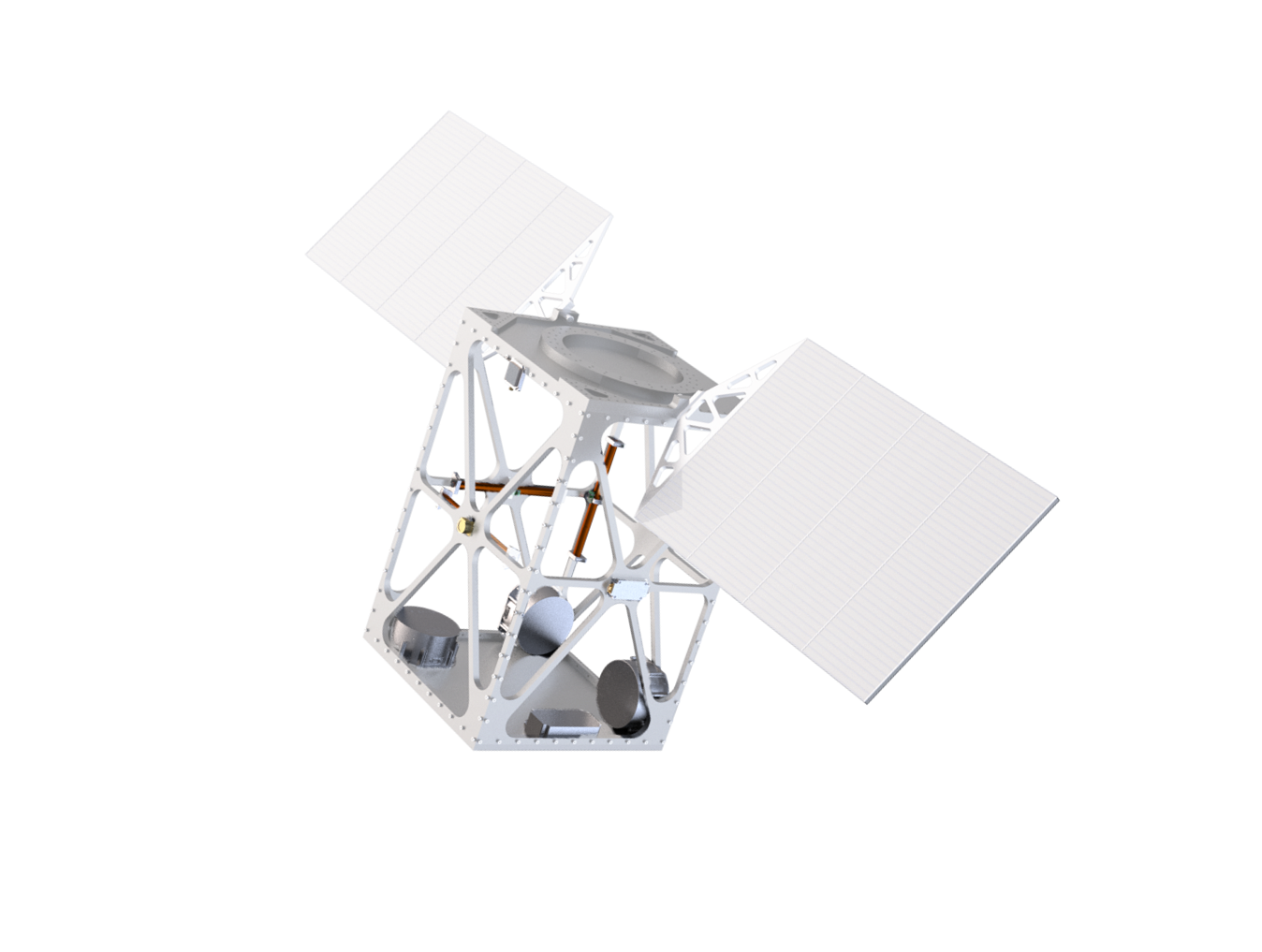
Problem Statement: Required to run environmental tests of their products
These are initially done during prototyping phase to identify potential failure points and improve on the design
Mimics the space rocket launch conditions
Ensure reliability of components – will they still be able to perform once they have reached orbit?
After vibration tests, observed failure of some of the leads on certain components
In particular, the main controller FPGA chip
Some other ICs were of concern as they were also critical components (though not yet failing)
NSS wanted to identify cause of problem, and test different actions to prevent these failures
What is Ansys Sherlock?
Electronics-focused, RELIABILITY prediction tool, with fast predictions, and detailed FEA analysis types
Powerful, pre- and post-processor for all engineers working in electronics hardware
Pre-Processor: Conversion of ECAD into 3D FEA with geometric and material properties
Post-Processor:
Reliability prediction based on temperature, stress, and strain
Manufacturability of electronics post-assembly
Conclusion:
Sherlock gave accurate predictions of the locations of failure, thereby giving great confidence in simulation results
Insights gained from the simulations:
Staking adhesive will be used
Mounting points will be redesigned, with more to be added to improve stiffness/reduce deflection
Related Posts